Renewing instead of buying new.
Reduce CO2 emissions by 90%.
More than 90% of the CO2 emissions for a newly produced saw blade are related to steel and transport. Less than 10% of the impact comes from reprocessing and soldering, for example, carbide teeth. By designing and manufacturing saw blades with a high-quality core, we can extend the product’s lifespan and offer both maintenance sharpening and retipping. In our circular service flow, we reuse the core of the saw blade up to 20 times, thus reducing our environmental impact by more than 90%.
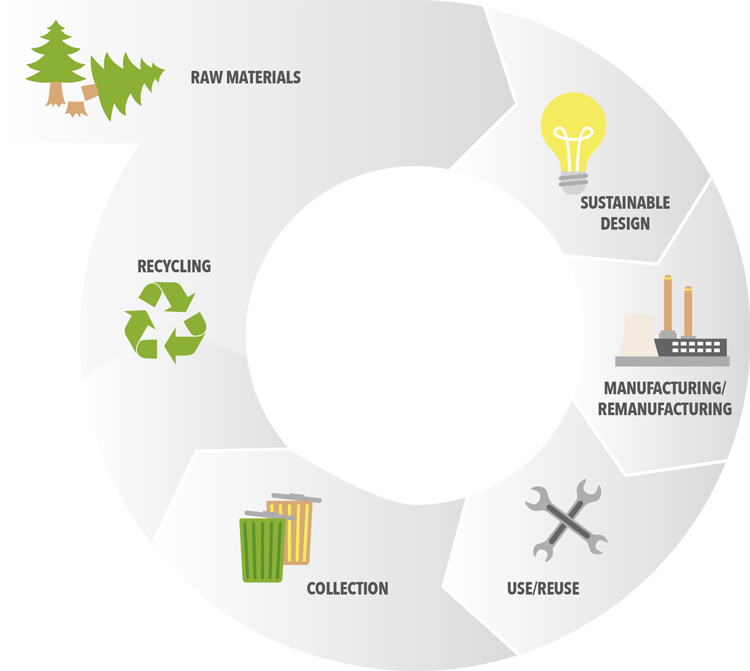
LSAB Group develops high-quality saw blades suitable for resharpening and retipping, focusing on uptime and TCO (Total Cost of Ownership).
100% of LSAB Group’s production takes place at facilities powered by renewable energy.
The products are designed to be sharpened and retipped at local service centers.
Customized transport with HVO (Hydrotreated Vegetable Oil) as fuel. Minimizes the environmental impact of service flow and product collection.
Expired products are collected for recycling. Automatic replacement ensures a high recycling rate.